Our Technology
Our Technology
Clean Energy Systems has developed revolutionary technology that is reshaping the power industry by eliminating the traditional exhaust stack and making zero-emission power a tangible reality.
OXY-FUEL COMBUSTION
What is it?
Oxy-fuel combustion has been the propulsion system of choice since the early days of rocket science. Defined as a combustion process in which fuel is mixed with an oxidizer such as pure oxygen, oxy-fuel combustion has been effectively used in solid, liquid, and gaseous combustion systems.
At the core of CES' technology is an oxy-fuel combustion system adapted from the same principles of rocket propulsion technology that power the American Space Shuttle. The CES combustor burns clean gaseous and/or liquid hydrocarbons with gaseous oxygen in the presence of recycled or even untreated produced water. It can burn a wide variety of fuels, including pipeline natural gas, high CO2 natural gas streams, syngas, landfill or bio-digester gas, and renewable fuels such as glycerin byproduct from biodiesel production.
How it works
CES’ oxy-fuel combustor outputs steam and CO2 which powers a conventional steam turbine to produce clean, firm power, and can also enable heat recovery for sale to a co-located industrial user. There is no need for post-combustion carbon capture, or cleaning of a flue gas stream, as the exit stream from the steam turbine is high-purity CO2 ready for sequestration or beneficial re-use in other industrial applications. CES technology is able to recover almost 100 percent of CO2 produced and release low-to-no criteria air pollutants, which is a game-changer for producing clean, firm power and heat using natural gas.
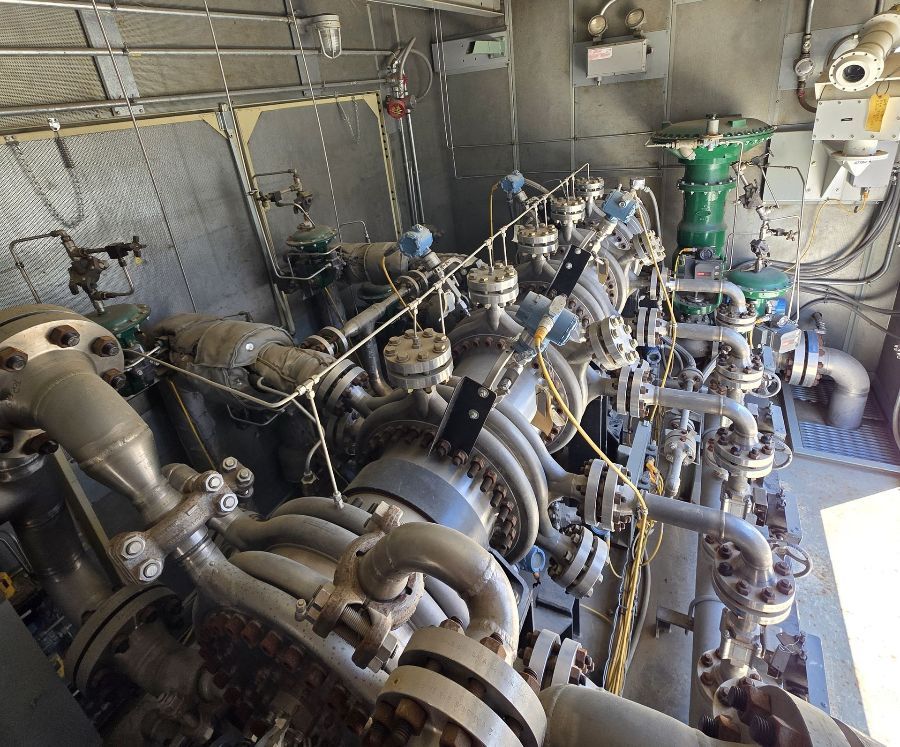
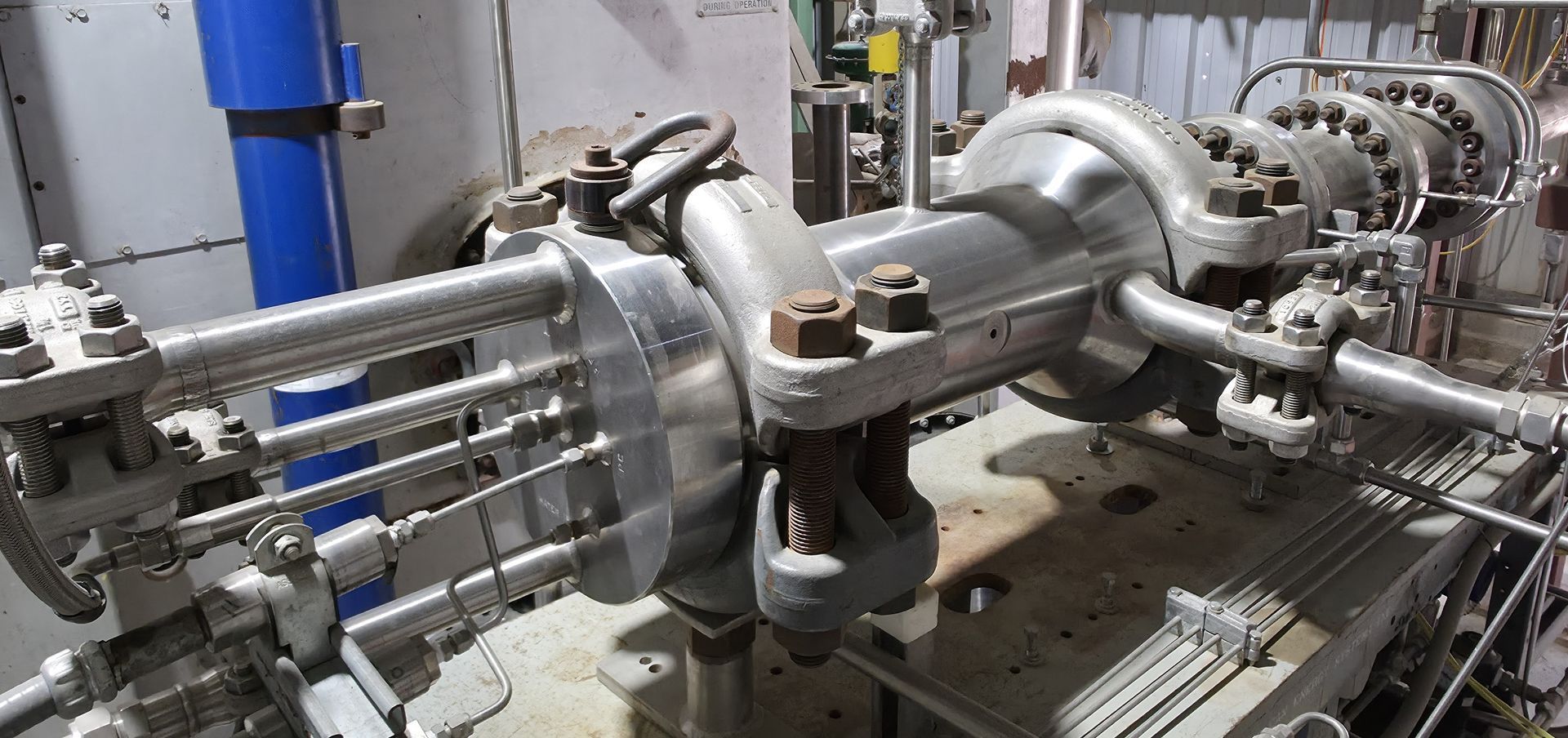
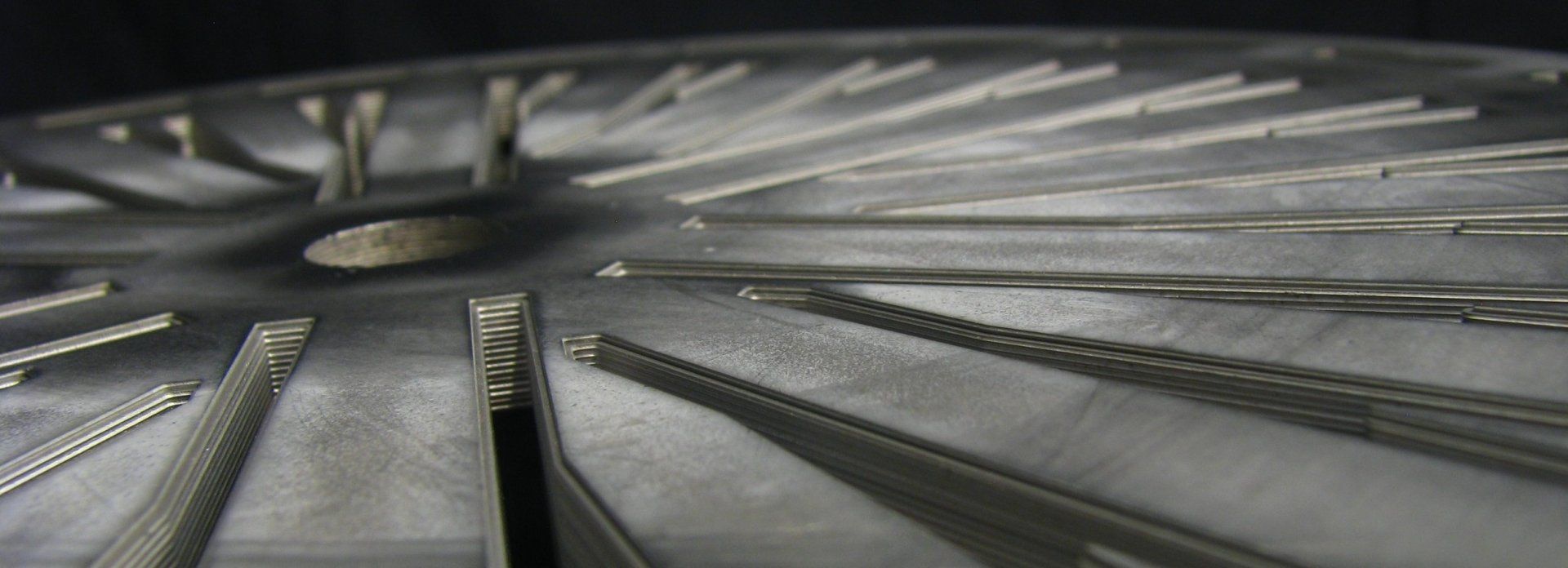
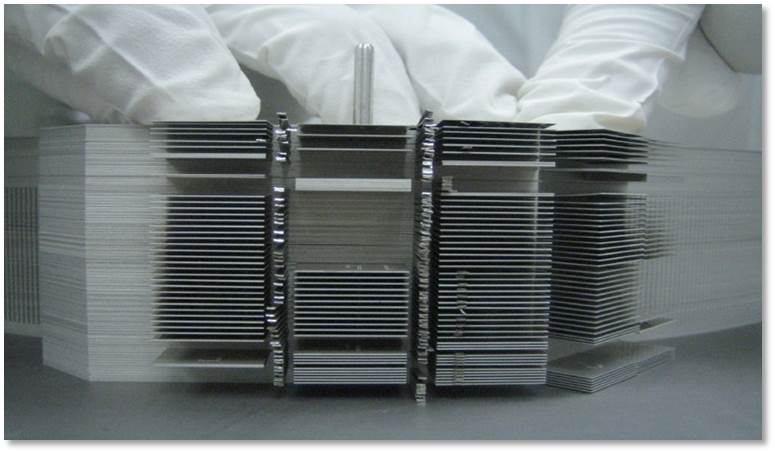
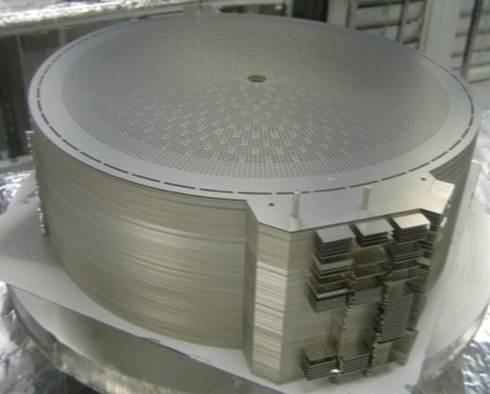
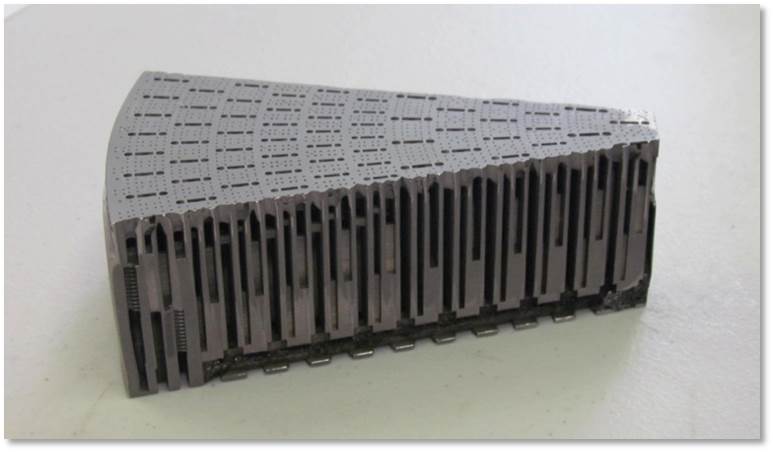
Platelet Technology
What is it?
A key difficulty in oxy-combustion is controlling the reaction, ensuring that the oxidizer and oxidant (fuel) mix to form a homogenous flame front, while avoiding hot spots or producing un-combusted product. To overcome this complication, CES developed platelet technology over a period of 20+ years as the basis for fabricating combustor injectors. CES has used platelets to engineer a highly precise, efficiently mixed, and controllable oxy-fuel combustion mechanism.
CES’ proprietary platelet technology provides solutions to difficult thermal and fluid flow problems in a variety of applications. To produce “platelets”, thin sheets of metal are chemically machined with photographic accuracy to produce specific patterns. These individual platelets are in turn accurately assembled and then joined by solid state diffusion bonding to form a monolithic structure containing internal passages. These passages contain precise flow control features and filters that effectively isolate and segregate the flows. Following bonding, the platelet assemblies are machined and welded using conventional techniques to produce finished products or components of assemblies.
Platelet technology plays an essential role in CES' oxy-fuel combustion systems - the heart of the CES' combustor, the injector, is a three-fluid platelet device. The CES platelet injector provides precise metering and mixing of fuel and oxidizer through hundreds of individual injection elements while providing the necessary cooling to assure long component life through the injection of water or steam.